Die casting is a flexible and popular manufacturing technique that creates intricate metal parts precisely. Hot and cold chamber die-casting are the main ways to form molten metal into complex components among the several die-casting methods. It is essential to comprehend the distinctions between these two procedures to choose the best approach for your unique production requirements.
This extensive blog will explore these two die-casting methods’ distinctions, the kinds of machines used, the drawbacks of hot chamber die-casting, and the importance of choosing the suitable die-casting machine for your particular requirements.
Difference b/w Hot Chamber and Cold Chamber Die Casting
The main difference is how hot chamber and cold chamber die-casting processes handle the molten metal. Let’s examine the primary distinction in more detail:
Hot Chamber Die Casting:

Low melting point metals like zinc, magnesium, and tin alloys are suitable for use with hot chamber die-casting equipment. Combining the die-casting machine and the furnace into one unit makes hot chamber die-casting unique. Because of this integration, there is always a ready supply of molten metal, significantly increasing process efficiency.
In a hot chamber die casting machine:
- The melted metal fills the metal reservoir, sometimes called the hot chamber.
- A crucial part that ensures accuracy and consistency is the plunger, which forces the molten metal into the mold.
- Usually constructed of sturdy materials like steel, the mold establishes the final product’s shape and size.
- Cooling passages inside the mold enable effective cooling.
- The two primary components of the die-casting machine are the moveable (ejector die) and fixed (cover die), which constitute the mold cavity.
Cold Chamber Die Casting:
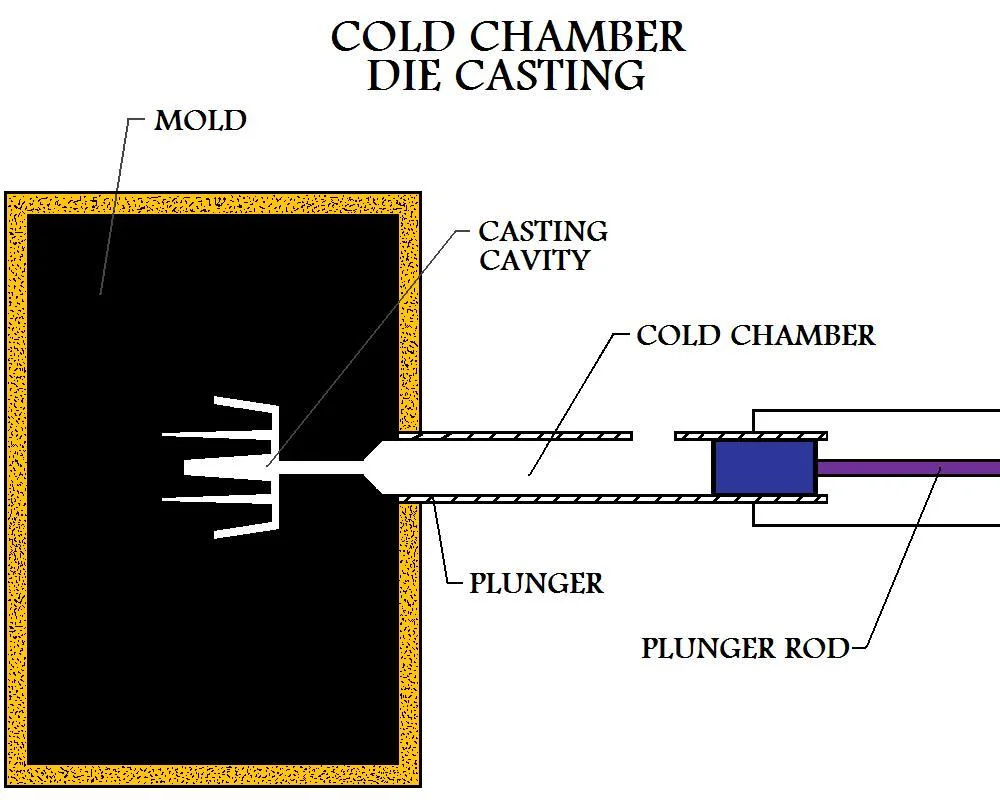
On the other hand, metals with higher melting points, such as alloys made of aluminum, are cast using cold chamber die-casting equipment. The critical distinction is that the die-casting machine and the furnace are different. It’s a labor-intensive method compared to hot chamber die casting because each cycle of the cold chamber machine requires ladling molten metal.
In a cold chamber die casting machine:
- Each cycle begins with a chilly chamber filled with molten metal.
- The plunger forces the metal into the mold for shaping, like in hot chamber die casting.
- The mold and cooling system remain similar to those used in hot chamber die casting.
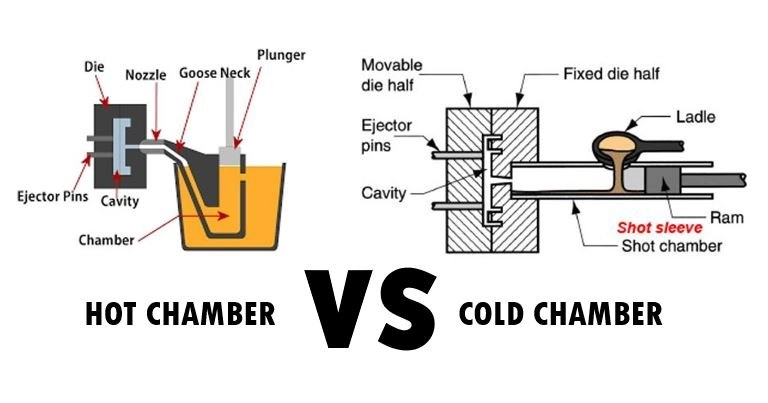
Secondary Differences Between Hot and Cold Chamber Die Casting
While the furnace setup remains the primary difference, hot and cold chamber die casting also exhibits variations in several aspects. Here’s a closer look at these secondary differences:
1. Cycle Times:
Due to its integration, hot chamber die casting typically boasts shorter cycle times, making it suitable for high-production environments.
Cold chamber die casting involves longer cycles due to the need for separate furnace operations, making it more suited for low to medium production quantities.
2. Materials:
Hot chamber die casting primarily employs metals with low melting points, including zinc, magnesium, and tin alloys.
Cold chamber die casting is known for its ability to handle metals with higher melting points, such as various aluminum alloys.
3. Safety Measures:
Hot chamber die casting is generally considered safer due to reduced molten metal movement and lower operating temperatures.
Cold chamber die casting demands more substantial worker and equipment safety investments due to handling metals at higher temperatures.
4. Investment Costs:
Cold chamber die casting often requires higher initial investments. This is attributed to the expenses associated with separate furnaces and die-casting setups, elevated energy costs, increased maintenance expenses from temperature-related wear and tear, and shorter tool life, which can incur high charges in die-casting operations.
Hot Chamber Die Casting Process Needs to be Suited For…
While hot chamber die casting offers several advantages, it is only suitable for some applications, primarily due to the limitations of using metals with lower melting points. Here are some scenarios where hot chamber die casting may not be the best choice:
- High Melting Point Metals: Hot chamber die casting machines must better suit metals with high melting points. Attempting to use them for such metals could damage the machine components.
- Large and Complex Parts: Due to handling constraints, hot chamber die casting is typically limited to smaller parts. Cold room die casting is preferred for larger and more complex components.
- Initial Tooling Investment: The initial tooling investment for hot chamber die casting can be substantial. Smaller businesses may need help to allocate the necessary resources.
- Safety Concerns: While hot chamber die casting is generally considered safe, it involves handling molten metal, which always carries some inherent risks. Adequate safety measures must be in place.
Selecting the Ideal Die Casting Machine
Choosing a suitable die casting machine is crucial for achieving high-quality results in your manufacturing process. Here are some key considerations when selecting between hot and cold chamber die-casting machines:
- Material Requirements
Start by evaluating the materials you intend to use for your components. A hot chamber die-casting machine is suitable if your project involves metals with low melting points, like zinc or magnesium. Conversely, opt for a cold chamber die-casting machine with metals like aluminum or copper alloys.
- Part Size and Complexity
Do consider the size and complexity of the parts you need to produce. Hot chamber die casting is efficient for smaller and less complex components. Cold chamber die casting is better equipped to handle the job if your project involves larger or more intricate parts.
- Initial Investment
Factor in your budget and resources when making a decision. Hot chamber die-casting machines are often more affordable upfront due to their integration and lower maintenance requirements. However, cold chamber machines offer versatility and are more appropriate for applications demanding structural integrity.
- Safety and Compliance
Safety should always be a top priority, regardless of your chosen die-casting method. Ensure that your chosen machine complies with industry standards for safety and performance. Additionally, provide thorough operator training and regular machine maintenance to guarantee safe and efficient operation.
Conclusion
If you work in the manufacturing sector, you should know the distinctions between hot and cold chamber die casting. Every tactic has benefits and drawbacks; therefore, choosing the ideal die-casting machine for your requirements is imperative.
Marcus High-Tech Engineering is a reliable industry partner offering various die-casting solutions and technical advice. Companies have greatly benefited from their knowledge and dedication to choosing the best die casting machines. By working with Marcus India, you can use their experience to make an investment that will meet your needs and goals exactly.
FAQs
Hot chamber die casting is a manufacturing process that produces metal parts by injecting molten metal into a mold cavity under high pressure. The injection mechanism is integrated with the die-casting machine, and the metal is stored in a furnace within the machine.
Cold chamber die casting is when molten metal is injected into a mold cavity from an external furnace or holding pot. Unlike hot chamber die casting, the metal injection system is separate from the die-casting machine.
Hot chamber die casting is primarily used for alloys with low melting points, such as zinc, tin, and lead.
Cold chamber die casting suits metals with higher melting points, including aluminum, magnesium, and copper alloys.
To request a quote or discuss your die casting needs with Marcus, please visit our website and fill out the contact form or visit the website at www.marcusindia.in.