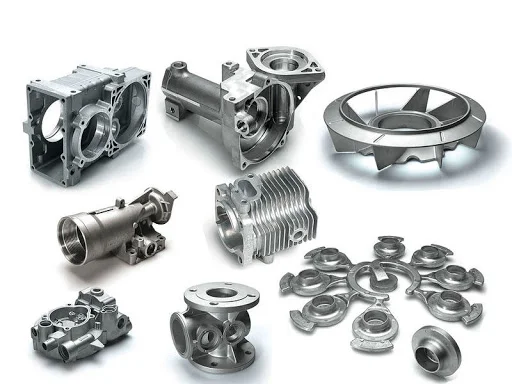
The die casting suppliers in India have experienced remarkable growth in recent years, propelled by the increasing need for high-quality metal components across diverse sectors. This expansion is fueled by rising automotive production, infrastructure development, and the growing demand for consumer goods. Industry reports indicate that the Indian die casting market is projected to reach a value of USD 1.81 billion by 2026, reflecting this sector’s immense potential and promising future.
The significant market size and anticipated growth have led to the emergence of several top-notch die casting suppliers in India. These suppliers have positioned themselves as key players in the industry by offering a combination of advanced technologies, superior quality standards, and reliable services. They have established strong manufacturing capabilities, state-of-the-art facilities, and stringent quality control processes to meet the ever-increasing demands of their clients.
In this article, we have listed the top 10 die casting suppliers in India, showcasing their distinctive features, areas of expertise, and contributions to the thriving manufacturing landscape.
Each supplier on this list has demonstrated excellence in their respective domains, serving diverse industries such as automotive, aerospace, electronics, and consumer goods. By exploring their capabilities, we aim to provide valuable insights into the leading players in the Indian die casting industry and shed light on their contributions to the country’s manufacturing prowess.
But first, let’s understand die casting across various sectors.
About Die Casting
Die casting is a highly versatile and efficient manufacturing process used to create intricate metal parts with excellent dimensional accuracy and surface finish. It involves injecting molten metal, typically aluminum, zinc, or magnesium, into a mold cavity at high pressure.
The molten metal fills the mold quickly and solidifies, resulting in a precise and detailed final product that takes on the shape of the mold. This method is highly advantageous for producing complex shapes at a high production rate and cost-effective manner, making it an ideal choice for various manufacturing needs.
Most common types of die casting
Aluminum Die Casting
Aluminum die casting is widely used in various industries due to the exceptional properties of aluminum, such as its lightweight nature, high strength-to-weight ratio, and excellent corrosion resistance. The process involves injecting molten aluminum into a steel mold designed to produce the desired shape of the final part.
Aluminum die casting is prevalent in the automotive industry for manufacturing engine components, transmission cases, and structural elements. It is also widely employed in the aerospace, electronics, and consumer goods sectors.
Zinc Die Casting
Zinc die casting is another prominent type that utilizes molten zinc instead of aluminum. Zinc is known for its excellent casting properties, ability to flow easily into intricate molds, and superior dimensional stability. Zinc die casting is highly valued for its high strength, durability, and superb electrical and thermal conductivity. It finds applications in various industries, including automotive (brackets, housings), electrical (connectors, switches), and hardware (locks, hinges).
Zinc die casting is favored when intricate details, thin walls, and excellent surface finishes are required.
Both aluminum and zinc die casting offer significant advantages over traditional manufacturing processes. They allow for high-volume production, reduce the need for secondary operations, and enable the production of complex shapes and thin walls. Additionally, die casting ensures consistent quality and dimensional accuracy, resulting in parts that fit together seamlessly and perform reliably.
The choice between aluminum and zinc die casting depends on several factors, including the specific requirements of the part, desired mechanical properties, cost considerations, and industrial applications. Both processes have proven efficient and reliable for producing components used in various sectors.
Whether aluminum die casting for lightweight and corrosion-resistant components or zinc die casting for high strength and intricate detailing, these processes continue revolutionizing industries such as automotive, aerospace, electronics, and beyond.
Top Die Casting Suppliers in India
1. Marcus
Marcus Hi Tech Engineering Pvt. Ltd is a reputable supplier specializing in aluminum and zinc die casting and machine components. They are known for their high-quality products that meet stringent industry standards. With expertise in die casting processes, Marcus Hi-Tech Engineering delivers durable, precise, and dimensionally accurate die castings suitable for various applications.
2. Fenfe Metallurgical
Fenfe Metallurgical is one of the prominent die casting suppliers in India known for high-precision defense components, large castings for the machine-building industry, pressure-tight castings for the HV transmission industry, and parts for hydraulics and power machines. Their commitment to producing high-quality and precise castings has earned them a reputation in the industry.
3. Rockman Industries
Rockman Industries has a rich history, starting as a bicycle manufacturer in the 1960s and now being a leading manufacturer of aluminum die casting parts. With five manufacturing units located in Haridwar, Ludhiana, Chennai, and Bawal, they have a strong annual capacity for aluminum processing. Rockman Industries specializes in gravity die casting, low-pressure die casting, and high-pressure die casting processes. They supply aluminum die casting components to renowned automobile OEMs globally.
4. Esko Die Casting Pvt Ltd
Esko Die Casting has been a trusted aluminum die casting component manufacturer since 1973. With operating facilities in Kolkata and Faridabad, Esko provides a wide range of cost-effective, high-quality aluminum and zinc-based high-pressure die cast components. They also offer gravity die cast components and comprehensive tool designing and development services to domestic and international customers.
5. Indian Diecasting Industries
Indian Diecasting Industries, established in 1964 in Aligarh, Uttar Pradesh, is a leading manufacturer of superior aluminum die cast components, zinc die cast components, and die casting molds. They use high-grade raw materials sourced from certified vendors, ensuring their products meet high performance and durability standards. Their range of components can be customized to meet specific client requirements.
6. Endurance Group
Endurance Group is a prominent die casting supplier in India, catering to the automotive industry. This company focuses on aluminum high-pressure die casting and produces vital automotive parts like engine blocks, transmission cases, and suspension components. With advanced technology and stringent quality control, Endurance Group ensures the delivery of reliable and durable die castings to renowned automobile manufacturers.
7. Sundaram Clayton Limited
Sundaram Clayton Limited (SCL) is India’s leading die casting supplier, primarily serving the automotive industry. They specialize in aluminum high-pressure die casting and supply critical components for engines, transmissions, and chassis systems. SCL has state-of-the-art manufacturing facilities and focuses on continuous improvement and technological advancements to meet the evolving needs of the automotive sector.
8. Menon Pistons Ltd
Menon Pistons Ltd is a renowned die casting supplier specializing in aluminum and zinc die castings for automotive and non-automotive applications. They offer many high-quality die-cast components, including pistons, cylinder heads, engine blocks, and electrical connectors. With a focus on innovation and customer satisfaction, Menon Pistons Ltd has established itself as a reliable supplier in the die casting industry.
9. Rane Die Cast Limited
Rane Diecast Limited is a top supplier of aluminum die castings to the automotive industry, with expertise in high-pressure and low-pressure die casting methods. They produce a range of components, including steering knuckles, suspension parts, and transmission housings. Quality control is a top priority for Rane Die Cast Limited, and they use advanced manufacturing techniques to meet the demanding standards of the automotive sector.
10. Sudharsan Heavy Engineering, Coimbatore
Sudharsan Heavy Engineering specializes in customized die casting solutions, manufacturing products, including self-lubricating bearings, split-type bearings, pressure handling parts, graphite-filled components, non-standard metal alloys, critical seals and assemblies, and critical shapes. Their expertise and focus on customization make them a reliable supplier in the Coimbatore region.
These additional top die casting suppliers in India showcase the diverse capabilities and contributions of the industry. With their expertise, advanced technology, and commitment to quality, they play a significant role in meeting the die casting needs of various sectors, particularly the automotive industry.
Die casting for various industries
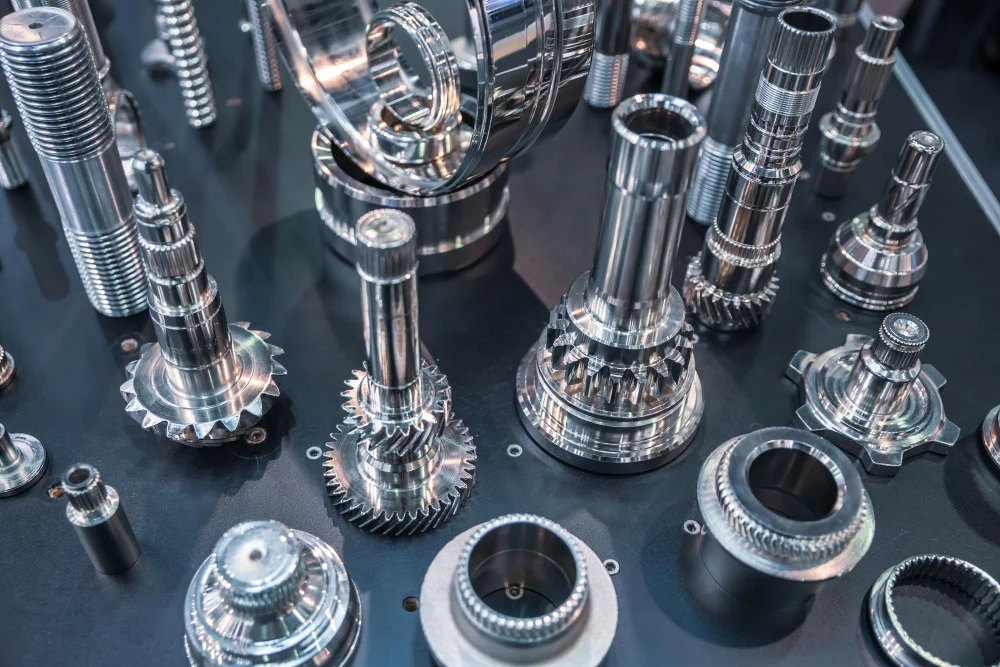
Die casting is a versatile manufacturing process that caters to a wide range of industries. Its ability to produce complex, high-quality metal parts with excellent dimensional accuracy makes it a preferred choice for various applications. Let’s explore some of the key industries that rely on die casting:
- Automotive Industry: Die casting plays a vital role in the automotive sector, where precision, strength, and lightweight components are crucial. It is used to manufacture engine blocks, transmission cases, cylinder heads, pistons, and other critical parts. Aluminum die casting is prevalent in the automotive industry due to its lightweight nature and excellent thermal conductivity.
- Aerospace Industry: The aerospace sector demands components that are lightweight and possess high strength and reliability. Die casting fulfills these requirements by producing intricate and complex parts in aircraft engines, landing gear systems, airframe structures, and other aerospace applications.
- Electronics and Electrical Industry: Die casting finds extensive use in the electronics and electrical sectors, where precise components with excellent electrical conductivity and heat dissipation properties are essential. Aluminum and zinc die castings are employed in producing connectors, housings, heat sinks, motor parts, and other electronic and electrical devices.
- Consumer Goods Industry: When it comes to consumer goods, die casting components are utilized widely, ranging from household appliances to furniture hardware. It allows for producing aesthetically pleasing, durable, and high-quality components used in products such as refrigerators, air conditioners, power tools, and decorative items.
- Industrial Equipment Industry: The industrial equipment sector relies on die casting to produce components used in machinery and equipment. Die castings provide the strength, precision, and dimensional stability required for industrial pumps, valves, hydraulic systems, power tools, and various industrial machinery parts.
- Medical Equipment Industry: Die casting is also employed in producing components used in the medical equipment industry. It ensures the manufacturing of intricate and sterile parts for medical devices and equipment, maintaining high precision and quality standards.
- Energy Sector: Die casting is a widely used manufacturing process in the energy sector. It is utilized to produce components for renewable energy systems like wind turbines and solar panels. This process ensures the creation of lightweight and durable parts that enhance the efficiency and sustainability of renewable energy generation.
- Automotive Industry: Die casting plays a vital role in the automotive sector, where precision, strength, and lightweight components are crucial. It is used to manufacture engine blocks, transmission cases, cylinder heads, pistons, and other critical parts. Aluminum die casting is prevalent in the automotive industry due to its lightweight nature and excellent thermal conductivity.
These are just a few examples of industries that benefit from die casting. The process’s versatility, precision, and efficiency make it a preferred choice across various sectors where high-quality metal components are required. By leveraging die casting technology, these industries can meet the demanding requirements of modern manufacturing and deliver reliable and superior products to their customers.
Also Check: Key Factors to Consider When Selecting Die Casting Suppliers in India
Final Words
The Indian die casting industry offers immense opportunities for suppliers and manufacturers. Throughout this blog, we have explored top 10 die casting suppliers in India, showcasing their expertise, capabilities, and contributions to various sectors.
All the die casting suppliers in India are dedicated to delivering top-notch products utilizing advanced technology and adhering to stringent quality control measures. They offer customization options to cater to the diverse needs of various industries, including automotive, aerospace, electronics, consumer goods, and the energy sector. Their expertise in aluminum and zinc die casting processes ensures that they produce lightweight and high-performance components that contribute to the growth and innovation of Indian manufacturing. These suppliers are critical in driving the country’s manufacturing sector forward, creating growth opportunities, and reinforcing India’s position as a global manufacturing hub.
FAQs
The largest die casting company in India is Marcus Hi-Tech Engineering Pvt Ltd. They are known for their expertise in die casting solutions and have a strong presence in the industry.
Die casting companies are manufacturing firms that specialize in producing metal parts and components using the die casting process.
Die casting can be expensive for several reasons:
High Initial Tooling Costs: The process requires the creation of complex molds, which can be costly to design and manufacture.
Material Costs: Die casting often uses specialized materials like aluminum, zinc, or magnesium alloys, which can be more expensive than standard materials.
Labor Intensive: Skilled operators are needed to set up and operate the machinery, leading to higher labor costs.
Quality Control: Strict quality control measures are essential to ensure the final products meet exact specifications, increasing overall costs.
Energy Consumption: Die casting machines require a significant amount of energy, contributing to operational expenses.
The three primary types of die casting are:
Cold Chamber Die Casting: In this method, molten metal is transferred to the die casting machine’s chamber from an external furnace. It is commonly used for alloys with high melting points, like aluminum and copper.
Hot Chamber Die Casting: This technique is suitable for low-melting-point alloys, such as zinc and magnesium. In hot chamber die casting, the molten metal is already within the machine, reducing the need for external melting furnaces.
Gravity Die Casting: Unlike the previous two methods, gravity die casting does not rely on high-pressure injection. Instead, molten metal is poured into a die using gravity. This process is ideal for thicker and more massive parts, often made from aluminum and other metals.